The company specializes in spray (spray) technology, also known as spray or spray welding (spray soldering) technology, which is a special treatment technology in surface treatment and has a wide range of applications. The basic principle is to melt the material (powder or wire) with energy such as flame, arc or plasma, then atomize it with high pressure airflow and attach it at high speed through high pressure airflow. By this special technique, the surface of the workpiece substrate is deposited and solidified to form a film thickness or a modified coating to adjust, change or enhance the properties of the surface of the substrate to achieve corrosion resistance, rust prevention, friction resistance and sliding resistance (Surface roughening), anti-stick process, high temperature oxidation resistance, insulation, heat insulation, thermal conductivity, wear resistance and biological activity.
Chengyiwang Industrial Co., Ltd. was established in 1979. The main equipment and process methods in the factory include plasma spray, high-speed flame spray, general flame spray, arc spray, flame wire and other technologies. Materials used such as spray-specific tungsten carbide, chromium carbide, ceramics (alumina, zirconia), silicon, porcelain gold (combination of ceramics and metals), metals (aluminum, zinc, copper, stainless steel), alloys (iron-based alloys, cobalt-base alloys, nickel-based alloys, superalloys) and the like. The material forms are powder, wire, bar, etc. Applications include aerospace, automotive, printing, paper, textile, plastic injection, petrochemical, electronic power, medical equipment, food equipment, machinery manufacturing and optoelectronic semiconductor equipment, and other related new product manufacturing and repair of old products. |
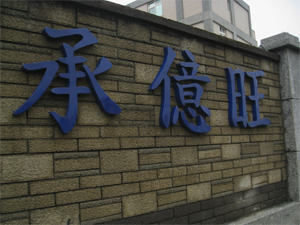
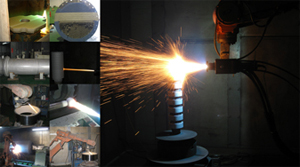 |
All solid engineering materials, including meal and alloy, ceramic and metal ceramic, plastics,
organic and inorganic materials, materials, non-crystal materials, and nano-materials are
used for painting uses.
2. Coating functions and diversifications
Different hot spray methods and materials are adopted to strengthen the surface of
work pieces.
3. Fast sedimentation, big spray thickness
The coating thickness is available from 50μm~5mm, compared with 0.1μm~10μm made
by PVD or CVD. Easy adjusting and control in thickness and composition, a feature in
comparison with other technologies.
4. Small substrate impacts
The temperature is maintained below 200∘c, an attempt to avoid substrate
transformations and surface changes from high temperature
5. Repairing
Hot coating enables to conduct surface treatment but also repair waste parts.
It also offers forming and produces machine parts directly.
6. Abrasive coating
Mainly used for turbine blades, abrasive coating includes nickel/graphite, aluminum/high
polymers or mixed materials (hard or soft).
7. Resumed size coating
Hot coating resumes the size due to shrinkage from machinery wearing, especially in
axes and rollers. This extends the life of machinery parts.
|